Automatic combine header transport kit

AGCO company

AGCO DYNAFLEX Flex Draper
Introduction
At the end of the day, farming is about efficiency. To meet this goal, manufacturers have designed larger combines and headers and have built the machines for quick setup and shutdown times. One area that has the potential to decrease setup time is the transport kit of headers. AGCO is a global company focusing on the design, manufacture, and distribution of agricultural equipment. Combine draper is one of their main products and they want to reduce the setup time for their headers. They currently have a manual transport kit that comes installed on the headers shown below. The transport kit requires an operator to lift the header with their combine, unpin the axles in the stored position, swing down axles from the stored position and pull into the road position, and finally pin the axles in the road-ready position. The front and the back wheels are arranged differently to account for turning and stability. The front wheels are more compact and require ninety-degree rotation when moving from stored to road position. The back wheels sit wider apart for stability. Now they need a new design to make the transport kit automatically.

New transport kit

Our design team with Agco engineers
Evaluation
Design Pro:
-
Whole transport kit can fold or unfold automatically
-
Meets the maximum height of the header
-
Stress in the design is below the maximum limit to hold the header
-
Easy functional with hydraulic cylinder
-
Cylinders easily accessible for maintenance
-
Compact design
-
A lot of similar parts from the manual kit
Weakness:​
-
von Mises stress close to material yielding stress
-
Larger deformation than expected on the frame
Overall:
As the designs are now, certain requirements have been met. The transport kit will not impede the ground when swinging. The design also has enough automation to classify as an automatic transport kit. Stresses are below yielding but will need to be further reduced to accommodate dynamic and unpredictable loading. Displacements will also need to be reduced in this process.
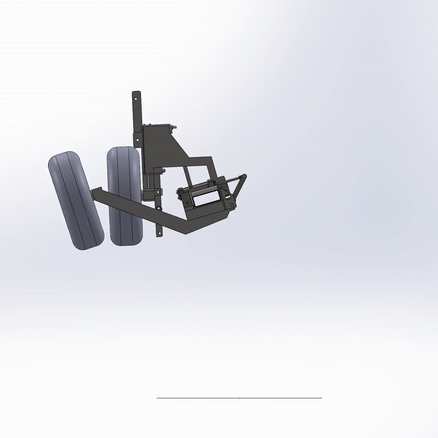
rear wheel Function

Front wheel function
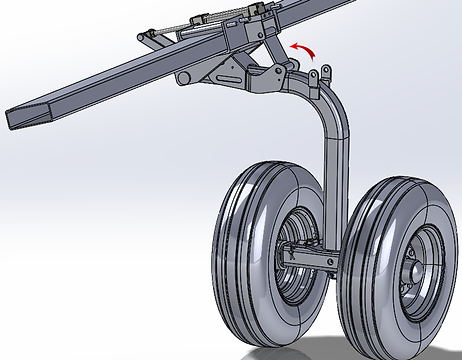
Front wheel assemable
Achievement
On the rear assembly, the wheels will be in the folded-out orientation as shown left in Animation. There will be a C-channel on the left side wheel to have a place to pin the frame and channel. The swing frame that swings to the right, it will be supported by two blocks on hooked to the frame, along with a rod or stop at the top to rest against. The frame sits at the same angle that the current design sits at, so the height of the kit shouldn’t be much different. Also, the two wheels are able to line up with no offset in the wheelbase. Both frames are operating with hydraulic cylinders.
For the front assembly, the cylinder extends to swing the frame from field mode to transport mode. As the cylinder extends, the linkage pulls a connection on the beam swinging the full assembly. In the transport mode, support is swung up (as shown by the red arrow) to connect to the header support bar. This support is to reinforce against torsion as the header is pulled. Most of the design on the front assembly was pulled from AGCO’s current manual kit. This is done due to the front assembly’s compact design, verified results, known manufacturability, and reduces as much need to train/setup manufacturing.
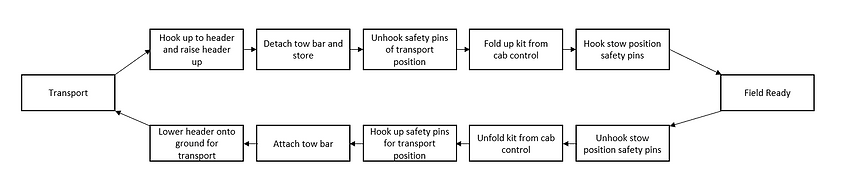
CURRENT design Function diagram
